Les avantages pour l'utilisateur sont :
- détection rapide des différences de phase (temps de réponse inférieur à 1 s)
- Remplacement des méthodes de détection manuelles, visuelles ou indirectes (par ex. temporisation)
- amélioration du rendement du produit
- économie de coûts d'énergie et de matériaux
- commande optimale de l'installation grâce à l'information en ligne sur l'état du processus
- sécurité accrue de l'installation grâce à une surveillance continue
L'utilisation des technologies numériques de traitement des signaux les plus modernes garantit une mesure extrêmement précise ainsi qu'une protection contre les perturbations de la vitesse absolue du son et de la concentration de différents fluides dans la séparation de phases. De plus, des capteurs de température intégrés, la construction sophistiquée du capteur et un savoir-faire acquis au cours d'innombrables séries de mesures et de nombreuses applications assurent une grande fiabilité du système avec de longues durées de fonctionnement.
Les avantages de la méthode de mesure sont les suivants :
- vitesse absolue du son en tant que grandeur physique univoque et traçable
- indépendante de la couleur, de la conductivité et de la transparence du liquide de process
- montage directement dans les tuyauteries et les réservoirs
- construction robuste du capteur, entièrement métallique, sans joints ni pièces mobiles
- sans entretien
- résistance à la corrosion grâce à l'utilisation de matériaux spéciaux
- utilisation à des températures allant jusqu'à 200 °C
- précision de mesure élevée et sans dérive, même en cas de forte proportion de bulles de gaz
- raccordement de jusqu'à quatre capteurs par contrôleur
- transmission des résultats de mesure par bus de terrain (Profi bus DP, Modbus), sorties analogiques, interface série ou Ethernet
La détection exacte des différentes phases dans une canalisation est nécessaire dans divers secteurs industriels. Souvent, les différents produits sont transportés par la même conduite, mais sont acheminés vers un endroit différent.
Dans les applications où, par exemple, le produit A est expulsé par le produit B, la phase intermédiaire doit être séparée séparément. Ainsi, dans les brasseries, différentes sortes de bières sont remplies l'une après l'autre, mais les circuits amont et aval sont séparés et réintroduits dans le processus de brassage.
Les aspects de sécurité jouent également un rôle dans les applications à haut potentiel de risque. La surveillance de la séparation des phases dans les pipelines multi-composants de l'industrie chimique, en particulier, fournit non seulement une information sur la qualité du produit (incoming goods), mais évite également un mauvais remplissage des réservoirs de stockage et donc des accidents graves.
Dans l'industrie pétrochimique, différents carburants sont transportés sur de très grandes distances dans une seule canalisation. Dans ce cas, la détection rapide des différents produits et la surveillance de leur qualité sont primordiales.
La séparation de deux phases peut être réalisée par des procédés batch. Dans ce cas, les liquides (par ex. l'eau et l'huile) se séparent en fonction de leurs propriétés physiques et chimiques.
Exemple d'application 1 : Organika
Au cours du processus de fabrication de produits cosmétiques, une séparation de phase a lieu, au cours de laquelle une phase saline, contenant beaucoup d'eau, est séparée d'un produit précurseur. Cette phase inférieure, riche en eau, est évacuée via la station d'épuration, où l'eau est traitée. Le précurseur produit, la phase supérieure, n'est biodégradable que dans une mesure limitée. Il est donc primordial d'éviter que cette matière polluante pour l'eau ne se retrouve dans les eaux usées. Afin de ne pas polluer l'eau dans les stations d'épuration, l'identification immédiate et fiable de la phase amont est une priorité absolue, afin d'éviter son introduction dans le système d'eaux usées par un arrêt rapide.
Les méthodes de mesure optiques sont exclues à ce stade, car différentes colorations peuvent apparaître lors de la séparation des phases. En outre, la séparation de phases peut entraîner la formation d'une couche de boue, ce qui, comme on le sait, peut s'avérer critique pour la mesure par effet de frontière optique en raison des effets d'encrassement.
Exemple d'application 2 : biodiesel / glycérine
La production de biodiesel génère de la glycérine comme sous-produit. Le mélange des deux substances est transporté dans de grands bacs de décantation et a ensuite plusieurs heures pour se séparer. Les capteurs LiquiSonic® sont généralement installés à la sortie du réservoir. En détectant la phase respective, la vanne est activée et le biodiesel et la glycérine sont dirigés vers le traitement ultérieur respectif. La phase intermédiaire retourne dans le processus de séparation.
1.3 Séparation des phases dans un processus continu
Dans un processus continu, la séparation d'un flux de processus est commandée par un ou plusieurs capteurs. Dans ce cas, seule la valeur de la vitesse du son caractéristique de la phase concernée est surveillée et maintenue constante.
Souvent, la concentration de produit de la phase porteuse varie dans l'alimentation. De ce fait, la hauteur de la limite de phase se déplace rapidement. Ainsi, la phase porteuse pourrait être retirée avec le produit, ce qui influencerait fortement la pureté. Du point de vue de la technique du procédé, la séparation des liquides s'effectue par une pompe dans chacune des deux conduites de sortie. De cette manière, il est par exemple possible de contrôler la séparation continue d'un mélange réactionnel.
Les avantages de la technique de mesure LiquiSonic® ne résident pas seulement dans le temps de réponse extrêmement rapide, inférieur à 1 s, mais aussi dans le raccordement de jusqu'à quatre capteurs à un seul contrôleur LiquiSonic®. Celui-ci traite toutes les valeurs de mesure et transmet les données au système de contrôle supérieur.
Selon le type de réservoir et les exigences, différentes variantes de montage sont possibles, comme le montre le graphique ci-dessous.
Variante de montage 1
Le plus souvent, les capteurs sont installés sur le côté du réservoir. La nécessité d'un capteur central (point de mesure 2) dépend de l'application et des caractéristiques de la phase intermédiaire.
Variante de montage 2
L'utilisation d'un seul capteur d'une longueur maximale de 4 m permet de déterminer le profil de phase de l'ensemble du réservoir. En fixant le capteur sur un chariot mobile, par exemple, et en combinaison avec un odomètre, les limites de phase peuvent être déterminées avec précision à leur hauteur actuelle.
Variante de montage 3 et 4
Dans les réservoirs où il n'y a pas de raccords sur le côté ou qui peuvent être réalisés ultérieurement, par exemple une double enveloppe chauffante, les capteurs sont positionnés au bon endroit directement ou via des tubes plongeurs. En cas d'utilisation de tubes plongeurs, l'électronique du capteur se trouve déportée à une distance pouvant atteindre 15 m à l'extérieur du réservoir.
2. Système LiquiSonic
2.1 LiquiSonic® 30
Le système LiquiSonic® se compose d'un ou de plusieurs capteurs et d'un contrôleur. Le capteur à ultrasons comprend la section de mesure à ultrasons ainsi que la détection très précise de la température. Chaque capteur fonctionne de manière autonome et peut être utilisé dans différentes applications. Les parties du capteur en contact avec les liquides sont en acier inoxydable DIN 1.4571 de manière standard.
La construction robuste et entièrement encapsulée ne nécessite aucun joint ou "fenêtre" d'application et ne nécessite donc aucun entretien. Différentes fonctions supplémentaires intégrées dans le capteur, comme le contrôleur de débit et la surveillance humide/sec, augmentent considérablement les avantages pour le client. La technologie haute performance LiquiSonic® garantit des résultats de mesure stables, même en présence d'une proportion élevée de bulles de gaz et d'une forte atténuation du signal par le liquide de process.
L'électronique spéciale du capteur se trouve dans un boîtier fermé moulé sous pression avec un indice de protection IP65. Si l'espace est limité, il est possible d'installer des capteurs avec une électronique déportée. Le contrôleur 30 gère les données de mesure et se charge de la visualisation. La commande s'effectue via l'écran tactile haute résolution. Grâce à l'intégration sûre dans le réseau, y compris le serveur web, le contrôleur peut être utilisé alternativement via un navigateur avec un PC ou une tablette.
La fonction d'ajustement permet d'adapter la valeur d'affichage aux valeurs de référence internes à l'entreprise. Les données de processus sont actualisées toutes les 250 millisecondes. Si les valeurs mesurées se situent en dehors de la plage limite, cela s'affiche à l'écran et un signal est immédiatement émis.
Les données de mesure peuvent être transmises à des commandes, des systèmes de contrôle de processus ou des PC via plusieurs sorties analogiques ou à relais librement modulables ainsi que via différentes interfaces de bus de terrain. Les données de mesure sont enregistrées dans le journal de données très complet. Il dispose de 2 Go pour les informations de processus et de 32 (99 en option) jeux de données de produits pour différents liquides de processus. Pour le traitement sur PC, ces données peuvent être lues via le réseau ou l'interface USB. En outre, il est facile de créer des protocoles de processus à des fins de documentation. En outre, un journal des événements est intégré au Controller 30. Il permet de documenter des événements tels qu'un changement manuel de produit, des modifications de configuration ou des messages d'avertissement et d'état.
2.2.2 Bus de terrain
L'option bus de terrain offre la possibilité d'intégrer le contrôleur dans un système de gestion de processus ou d'automatiser le déroulement du processus au moyen d'une commande (API). Outre la transmission de valeurs de mesure telles que la concentration ou la température, il est également possible d'échanger des paramètres et des données de commande (par ex. commutation de produit).
Le contrôleur prend en charge différents systèmes de bus de terrain et suit les normes recommandées par les organisations de normalisation respectives. Les variantes courantes sont Modbus et Profibus DP.
3. Qualité et service
L'enthousiasme pour le progrès technologique est notre force motrice pour contribuer à façonner le marché de demain. Vous, nos clients, êtes au centre de nos préoccupations. Nous nous engageons à vous fournir des prestations de haut niveau. En étroite collaboration avec vous, nous nous engageons sur la voie de l'innovation - en développant la réponse adéquate à votre tâche de mesure exigeante ou en procédant à des adaptations individuelles du système. La complexité croissante des exigences spécifiques aux applications rend indispensable une compréhension globale des relations et des interactions.
La recherche créative est un autre pilier de notre entreprise. Les spécialistes de notre équipe de recherche et de développement apportent ainsi une contribution précieuse à l'optimisation des caractéristiques des produits - comme l'essai de nouveaux designs de capteurs et de matériaux ou la fonctionnalité bien pensée des composants électroniques, matériels et logiciels. Notre gestion de la qualité SensoTech n'accepte que les meilleures performances, même dans la production. Depuis 1995, nous sommes certifiés ISO 9001. Tous les composants des appareils sont soumis à de multiples procédures de contrôle aux différentes étapes de la fabrication ; les systèmes sont déjà soumis à une procédure de burn-in dans notre entreprise. Notre maxime : fonctionnalité, résistance et sécurité maximales.
Tout cela n'est possible que grâce à l'engagement et au sens aigu de la qualité de nos collaborateurs. Nous devons notre succès à leurs excellentes connaissances techniques et à leur motivation. Ensemble, avec passion et conviction, nous travaillons avec une excellence qui n'a pas son pareil.
Nous soignons les relations avec nos clients. Comme nos appareils ne nécessitent pas d'entretien, nous pouvons nous concentrer entièrement sur vos besoins en matière de service et vous soutenir activement par des conseils professionnels, une installation confortable en interne et des formations pour les clients. Dans la phase de conception, nous analysons les conditions de votre situation directement sur place et effectuons des mesures d'essai si nécessaire. Nos appareils de mesure sont en mesure d'atteindre une précision et une fiabilité maximales, même dans des conditions défavorables. Même après l'installation : nous sommes là pour vous, nos temps de réaction sont courts - grâce à des options d'accès à distance spécifiquement adaptées à vos besoins.
Dans le cadre de nos coopérations internationales, nous formons pour nos clients une équipe au réseau mondial qui assure un conseil et un service optimaux dans tous les pays. C'est pourquoi nous attachons une grande importance à une gestion efficace des connaissances et des qualifications. Nos nombreuses représentations internationales sur tous les principaux marchés géographiques du monde peuvent s'appuyer sur les connaissances d'experts au sein de l'entreprise et actualisent continuellement leurs compétences dans le cadre de programmes de formation continue axés sur les applications et la pratique. La proximité avec le client, partout dans le monde : outre notre vaste expérience sectorielle, c'est un facteur clé de notre présence réussie dans le monde entier.
Une technologie de détection innovante
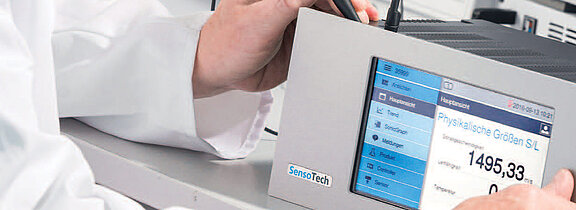
SensoTech est le spécialiste de l'analyse et de l'optimisation des processus techniques dans les liquides. Depuis sa création en 1990, nous sommes devenus une entreprise leader dans le domaine des appareils de mesure pour la détermination en ligne des concentrations dans les liquides. Nos systèmes d'analyse déterminent la tendance - dans le monde entier.
Ingénierie innovante made in Germany, dont le principe est la mesure de la vitesse absolue du son dans le processus en cours. Une méthode que nous avons perfectionnée pour en faire une technologie de détection extrêmement précise et exceptionnellement facile à utiliser.
Outre la mesure de la concentration et de la densité, les applications typiques sont la détection de phase ou le suivi de réactions complexes comme la polymérisation et la cristallisation. Nos systèmes de mesure et d'analyse LiquiSonic® garantissent une qualité optimale des produits, une sécurité maximale des installations ou réduisent les coûts grâce à une gestion efficace des ressources dans les secteurs les plus divers, tels que l'industrie chimique et pharmaceutique, la sidérurgie, la technologie alimentaire, la construction de machines et d'installations, la technique automobile et bien d'autres encore.
Nous voulons que vous puissiez exploiter pleinement le potentiel de vos installations de production à tout moment. Les systèmes de SensoTech fournissent des résultats de mesure très précis, même dans des conditions de processus difficiles, de manière exacte et reproductible. Et ce, en ligne et sans prélèvements d'échantillons critiques pour la sécurité, immédiatement disponibles pour votre système d'automatisation. Tous les paramètres du système peuvent en outre être adaptés à l'aide d'outils de configuration puissants, afin que vous puissiez réagir immédiatement et facilement aux changements.
Nous proposons ainsi une technologie excellente et sophistiquée pour améliorer vos processus de fabrication et sommes un partenaire pour des solutions exigeantes et souvent insoupçonnées dans votre secteur, pour vos applications, aussi spécifiques soient-elles. Lorsqu'il s'agit de liquides, c'est nous qui fixons les normes.