Phasentrennung
Nutzen für den Anwender sind:
- schnelle Detektion von Phasenunterschieden (Ansprechzeiten von kleiner 1 s)
- Ablösung manueller, visueller oder indirekter Detektionsverfahren (z. B. Zeitsteuerung)
- Verbesserung der Produktausbeute
- Einsparung von Energie- und Materialkosten
- optimale Anlagensteuerung durch Online-Information über den Prozesszustand
- erhöhte Anlagensicherheit durch kontinuierliche Überwachung
Die Verwendung modernster digitaler Signalverarbeitungstechnologien garantiert eine äußerst genaue sowie störsichere Messung der absoluten Schallgeschwindigkeit und Konzentration verschiedener Medien in der Phasentrennung. Zusätzlich sichern integrierte Temperatursensoren, die ausgefeilte Sensorkonstruktion und ein in unzähligen Messreihen und vielen Anwendungen gewachsenes Know-How eine hohe Zuverlässigkeit des Systems mit langen Laufzeiten.
Die Vorteile des Messverfahrens sind:
- absolute Schallgeschwindigkeit als eindeutige und rückführbare physikalische Größe
- unabhängig von Farbe, Leitfähigkeit und Transparenz der Prozessflüssigkeit
- Einbau direkt in Rohrleitungen und Behälter
- robuste Sensorkonstruktion in komplett metallischer Ausführung ohne Dichtungen oder bewegliche Teile
- wartungsfrei
- Korrosionsbeständigkeit durch Verwendung von Sondermaterialien
- Einsatz bei Temperaturen bis 200 °C
- hohe, driftfreie Messgenauigkeit auch bei hohem Gasblasenanteil
- Anschluss von bis zu vier Sensoren pro Controller
- Weiterleitung der Messergebnisse über Feldbus (Profi bus DP, Modbus), analoge Ausgänge, serielle Schnittstelle oder Ethernet
1. Prozess
1.1 Phasentrennung in der Rohrleitung
Die exakte Erkennung unterschiedlicher Phasen in einer Rohrleitung ist in diversen Industriebereichen notwendig. Oft werden die unterschiedlichen Produkte durch dieselbe Leitung gefördert, jedoch jeweils einem anderen Ort zugeführt.
Bei Anwendungen, in denen zum Beispiel Produkt A durch Produkt B ausgeschoben wird, ist die Zwischenphase gesondert zu trennen. So werden in Brauereien unterschiedliche Biersorten nacheinander abgefüllt, jedoch die Vor- und Nachläufe ausgekreist und dem Brauprozess wieder zugeführt.
Auch Sicherheitsaspekte spielen bei Anwendungen mit hohem Risikopotenzial eine Rolle. Besonders die Überwachung der Phasentrennung in Mehrstoffpipelines der chemischen Industrie liefert nicht nur eine Aussage über die Produktqualität (incoming goods), sondern vermeidet auch eine Fehlbefüllung der Lagertanks und somit schwerwiegende Unfälle.
In der Petrochemie werden unterschiedliche Kraftstoffe über sehr große Distanzen in nur einer Rohr-leitung gefördert. Hier stehen sowohl die schnelle Erkennung der unterschiedlichen Produkte als auch deren Qualitätsüberwachung im Vordergrund.
1.2 Phasentrennung im Batch-Prozess
Die Separation zweier Phasen kann verfahrenstechnisch in Batch-Prozessen erfolgen. Hier trennen sich die Flüssigkeiten (z.B. Wasser und Öl) aufgrund ihrer physikalischen und chemischen Eigenschaften voneinander.
Applikationsbeispiel 1: Organika
Während des Herstellungsprozesses von Kosmetika kommt es zu einer Phasentrennung, bei der eine salzhaltige Phase, die viel Wasser enthält, von einem Vorprodukt getrennt wird. Diese wasserreiche, untere Phase wird über die Kläranlage abgeleitet, wo das Wasser behandelt wird. Das erzeugte Vorprodukt, die obere Phase, ist nur in einem beschränkten Maß biologisch abbaubar. Daher ist es von größter Wichtigkeit, zu verhindern, dass dieses wasserbelastende Material in das Abwasser gelangt. Um das Wasser in den Kläranlagen nicht zu belasten, ist die sofortige und zuverlässige Identifikation der Vorprodukt-Phase von höchster Priorität, um eine Zuführung zum Abwassersystem durch eine rasche Abschaltung zu verhindern.
Optische Messverfahren scheiden an dieser Stelle aus, weil bei der Phasentrennung unterschiedliche Färbungen auftreten können. Weiterhin kann es bei der Phasentrennung zur Ausbildung einer Mulmschicht kommen, was bekanntermaßen durch Verschmutzungseffekte für die Messung über optische Grenzeffekte kritisch sein kann.
Applikationsbeispiel 2: Biodiesel / Glycerin
Bei der Herstellung von Biodiesel fällt Glycerin als Nebenprodukt an. Das Gemisch beider Stoffe wird in großen Absetzbehältern gefördert und hat anschließend mehrere Stunden Zeit sich zu separieren. Die LiquiSonic® Sensoren werden meist im Auslass des Behälters installiert. Durch die Erkennung der jeweiligen Phase wird das Ventil angesteuert und der Biodiesel und das Glycerin der jeweiligen Weiterverarbeitung zugeführt. Die Zwischenphase kehrt zurück in den Trennprozess.
1.3 Phasentrennung im kontinuierlichen Prozess
In einem kontinuierlichen Prozess wird über einen oder mehrere Sensoren die Trennung eines Prozessstroms gesteuert. In diesem Fall wird lediglich der für die jeweilige Phase charakteristische Schallgeschwindigkeitswert überwacht und konstant gehalten.
Oft schwankt die Produktkonzentration der Trägerphase im Zulauf. Dadurch verschiebt sich schnell die Höhe der Phasengrenze. So könnte die Trägerphase mit dem Produkt abgezogen werden, was die Reinheit stark beeinflusst. Verfahrenstechnisch erfolgt die Trennung der Flüssigkeiten über jeweils eine Pumpe in den beiden Auslassleitungen. Auf diese Weise lässt sich beispielsweise die kontinuierliche Trennung eines Reaktionsgemisches steuern.
Die Vorteile der LiquiSonic® Messtechnik liegen nicht nur in der extrem schnellen Ansprechzeit von kleiner 1s, sondern auch im Anschluss von bis zu vier Sensoren an nur einem LiquiSonic® Controller. Dieser verarbeitet alle Messwerte und leitet die Daten an das übergeordnete Leitsystem weiter.
Je nach Behältertyp und Anforderungen sind unterschiedliche Einbauvarianten möglich, die in der unten abgebildeten Grafik dargestellt sind.
Einbauvariante 1
Am häufigsten werden die Sensoren an der Seite des Behälters installiert. Die Erfordernis des mittle-ren Sensors (Messstelle 2) hängt von der Applikation und Ausprägung der Zwischenphase ab.
Einbauvariante 2
Bei der Verwendung von nur einem Sensor mit einer Länge von bis zu 4 m kann das Phasenprofil des gesamten Behälters bestimmt werden. Durch die Befestigung des Sensors auf einem beispielsweise beweglichen Schlitten und in Kombination mit einem Wegmesser können die Phasengrenzen exakt in ihrer aktuellen Höhe bestimmt werden.
Einbauvariante 3 und 4
In Behältern, in denen keine Anschlüsse an der Seite vorhanden sind oder nachträglich realisiert werden können, z. B. beheizbarer Doppelmantel, werden die Sensoren direkt oder über Tauchrohre an der richtigen Stelle positioniert. Bei der Verwendung von Tauchrohren befindet sich die Sensorelektronik abgesetzt in einer Entfernung von bis zu 15 m außerhalb vom Behälter.
2. LiquiSonic® System
2.1 LiquiSonic® 30
Das LiquiSonic® System besteht aus einem oder mehreren Sensoren und einem Controller. Der Ultraschallsensor beinhaltet die Ultraschall-Messstrecke sowie die hochgenaue Temperaturerfassung. Jeder Sensor arbeitet autark und kann in unterschiedlichen Applikationen betrieben werden. Die flüssigkeitsberührenden Teile des Sensors bestehen standardmäßig aus Edelstahl DIN 1.4571.
Die robuste und vollständig gekapselte Konstruktion benötigt keine Dichtungen oder „Fenster“ zur Anwendung und ist somit vollständig wartungsfrei. Verschiedene im Sensor integrierte Zusatzfunktionen wie der Strömungswächter und die Nass-/Trockenüberwachung erhöhen deutlich den Kundenutzen. Die LiquiSonic® Hochleistungstechnologie gewährleistet stabile Messergebnisse, selbst bei erhöhtem Gasblasenanteil und starker Signaldämpfung durch die Prozessflüssigkeit.
Die spezielle Sensorelektronik befindet sich in einem geschlossen Druckgussgehäuse mit Schutzart IP65. Bei geringem Platzangebot können Sensoren mit abgesetzter Elektronik installiert werden. Der Controller 30 verwaltet die Messdaten und übernimmt die Visualisierung. Die Bedienung erfolgt über das hochauflösende Touchdisplay. Durch die sichere Netzwerkintegration inklusive Webserver kann der Controller alternativ über Browser mit einem PC oder Tablet bedient werden.
Durch Justierfunktion kann der Anzeigewert an betriebsinterne Referenzwerte angepasst werden. Die Prozessdaten werden im 250 Millisekundentakt aktualisiert. Bewegen sich die Messwerte außerhalb des Grenzbereichs, wird dies im Display angezeigt und es erfolgt sofort ein Signal.
Die Messdaten können über mehrere frei skalierbare analoge oder Relais-Ausgänge sowie über verschiedene Feldbusschnittstellen an Steuerungen, Prozessleitsysteme oder PCs übertragen werden. Im umfangreichen Datenlogbuch werden die Messdaten gespeichert. Es stehen 2 GB für Prozessinformationen und 32 (optional 99) Produktdatensätze für verschiedene Prozessflüssigkeiten zur Verfügung. Zur Verarbeitung am PC, können diese über Netzwerk oder USB-Schnittstelle ausgelesen werden. Darüber hinaus lassen sich Prozessprotokolle für Dokumentationszwecke leicht erstellen. Ergänzend ist im Controller 30 ein Ereignislogbuch integriert. Darin werden Ereignisse wie ein manueller Produktwechsel, Konfigurationsänderungen oder Warn- und Statusmeldungen dokumentiert.
2.2.2 Feldbus
Die Feldbusoption bietet die Möglichkeit den Controller in ein Prozessleitsystem zu integrieren oder mittels Steuerung (SPS) den Prozessablauf zu automatisieren. Neben der Übertragung von Messwerten wie Konzentration oder Temperatur, können auch Parameter und Steuerdaten (z. B. Produktumschaltung) ausgetauscht werden.
Der Controller unterstützt verschiedene Feldbussysteme und folgt den von den jeweiligen Normungsorganisationen empfohlenen Standards. Als gängige Varianten gelten Modbus und Profibus DP.
3. Qualität und Service
Begeisterung für technologischen Fortschritt ist unsere treibende Kraft, den Markt von morgen mitzugestalten. Dabei stehen Sie, unsere Kunden, im Mittelpunkt. Ihnen gegenüber fühlen wir uns zu Höchstleistung verpflichtet. In enger Zusammenarbeit mit Ihnen gehen wir den Weg der Innovation – indem wir die passende Antwort auf Ihre anspruchsvolle Messaufgabe entwickeln oder individuelle Systemanpassungen durchführen. Die steigende Komplexität der applikationsspezifischen Anforderungen macht dabei ein umfassendes Verständnis für Zusammenhänge und Wechselwirkungen unerlässlich.
Kreative Forschung ist eine weitere, tragende Säule unseres Unternehmens. So leisten die Spezialisten unseres Forschungs- und Entwicklungsteams Wertvolles zur Optimierung von Produkteigenschaften – wie die Erprobung neuartiger Sensordesigns und Materialien oder die durchdachte Funktionalität von Elektronik, Hard- und Softwarekomponenten. Unser SensoTech-Qualitätsmanagement akzeptiert auch in der Produktion nur Bestleistungen. Seit 1995 sind wir nach ISO 9001 zertifiziert. Alle Gerätekomponenten durchlaufen in den verschiedenen Fertigungsstufen vielfältige Prüfprozeduren; die Systeme werden bereits in unserem Hause einer Burn-in-Prozedur unterzogen. Unsere Maxime: höchste Funktionalität, Belastbarkeit und Sicherheit.
All dies ist nur möglich durch den Einsatz und das ausgeprägte Qualitätsbewusstsein unserer Mitarbeiter. Ihrem ausgezeichneten Fachwissen und ihrer Motivation verdanken wir unseren Erfolg. Zusammen, mit Leidenschaft und Überzeugung, arbeiten wir mit Exzellenz, die ihresgleichen sucht.
Wir pflegen die Beziehungen zu unseren Kunden. Sie gründen auf Partnerschaft und gewachsenes Vertrauen. Da unsere Geräte wartungsfrei arbeiten, können wir uns in puncto Service ganz auf Ihre Anliegen kon-zentrieren und unterstützen Sie aktiv durch professionelle Beratung, komfortable Inhouse-Installation sowie Kundenschulungen. In der Konzeptionsphase analysieren wir Ihre Situationsbedingungen direkt vor Ort und führen gegebenenfalls Testmessungen durch. Unsere Messgeräte sind in der Lage, auch unter ungünstigen Konditionen höchste Genauigkeit und Zuverlässigkeit zu erzielen. Auch nach der Installation: Wir sind für Sie da, unsere Reaktionszeiten sind kurz – dank spezifisch auf Sie abgestimmter Fernzugriffsoptionen.
Im Zuge unserer internationalen Kooperationen bilden wir ein global vernetztes Team für unsere Kunden, das optimale Beratung und Service länderübergreifend sicherstellt. Wir legen deshalb Wert auf effektives Wissens- und Qualifikationsmanagement. Unsere zahlreichen internationalen Vertretungen in allen wichtigen geografischen Märkten der Welt können auf das Expertenwissen innerhalb des Unternehmens zurückgreifen und aktualisieren kontinuierlich, in applikations- und praxisbezogenen Weiterbildungsprogrammen, ihre Kompetenz. Die Nähe zum Kunden, rund um den Globus: neben der umfassenden Branchenerfahrung ein Schlüsselfaktor für unsere erfolgreiche Präsenz weltweit.
Innovative Sensortechnologie
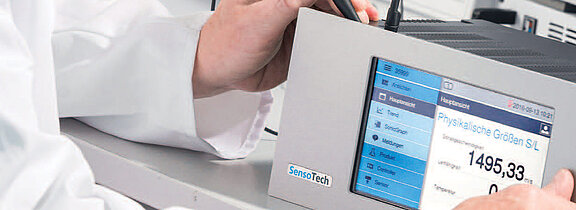
SensoTech ist der Spezialist für die Analyse und Optimierung verfahrenstechnischer Prozesse in Flüssigkeiten. Seit der Gründung 1990 haben wir uns zum führenden Unternehmen für Messgeräte zur Inline-Bestimmung von Konzentrationen in Flüssigkeiten entwickelt. Unsere Analysesysteme bestimmen den Trend – weltweit.
Innovatives Engineering made in Germany, dessen Prinzip die Messung der absoluten Schallgeschwindigkeit im laufenden Prozess ist. Eine Methode, die wir zu einer höchst präzisen und außergewöhnlich bedienerfreundlichen Sensortechnologie perfektioniert haben.
Typische Anwendungen neben der Konzentrations- und Dichtemessung sind die Phasendetektion oder die Verfolgung von komplexen Reaktionen wie Polymerisation und Kristallisation. Unsere LiquiSonic® Mess- und Analysesysteme sorgen für optimale Produktqualität, für höchste Anlagensicherheit oder senken durch effizientes Ressourcenmanagement die Kosten in den unterschiedlichsten Branchen, wie chemische und pharmazeutische Industrie, Stahlindustrie, Lebensmitteltechnologie, Maschinen- und Anlagenbau, Fahrzeugtechnik und weiteren.
Wir wollen, dass Sie die Potenziale Ihrer Produktionsanlagen zu jedem Zeitpunkt voll ausschöpfen. Systeme von SensoTech liefern hochgenaue Messergebnisse auch unter schwierigen Prozessbedingungen, exakt und reproduzierbar. Und dies Inline und ohne sicherheitskritische Probenentnahmen, sofort verfügbar für Ihr Automatisierungssystem. Alle Systemparameter lassen sich außerdem mit leistungsstarken Konfigurationstools anpassen, damit Sie sofort und unkompliziert auf Veränderungen reagieren können.
Wir bieten damit exzellente, ausgereifte Technologie zur Verbesserung Ihrer Herstellungsprozesse und sind Partner für anspruchsvolle, oft ungeahnte Lösungsansätze in Ihrer Branche, für Ihre Anwendungen – seien sie noch so spezifisch. Wenn es um Flüssigkeiten geht, setzen wir die Maßstäbe.