Las ventajas para el usuario son
- Detección rápida de las diferencias de fase (tiempos de respuesta inferiores a 1 s)
- Sustitución de métodos de detección manuales, visuales o indirectos (por ejemplo, control de tiempo)
- Mejora del rendimiento del producto
- Ahorro en costes de energía y material
- Control optimizado del sistema gracias a la información en línea sobre el estado del proceso
- Aumento de la seguridad de la planta gracias a la supervisión continua
El uso de las más modernas tecnologías de procesamiento digital de señales garantiza una medición extremadamente precisa y sin interferencias de la velocidad sónica absoluta y de la concentración de los distintos medios en la separación de fases. Además, los sensores de temperatura integrados, el sofisticado diseño de los sensores y la experiencia adquirida en innumerables series de mediciones y muchas aplicaciones garantizan un sistema altamente fiable con una larga vida útil.
Las ventajas del método de medición son
- Velocidad sónica absoluta como magnitud física clara y trazable
- Independiente del color, la conductividad y la transparencia del líquido de proceso
- Instalación directa en tuberías y recipientes
- Construcción robusta del sensor en un diseño completamente metálico sin juntas ni piezas móviles
- Sin mantenimiento
- Resistencia a la corrosión gracias al uso de materiales especiales
- Utilización a temperaturas de hasta 200 °C
- Elevada precisión de medición sin desviaciones, incluso con alto contenido de burbujas de gas
- Conexión de hasta cuatro sensores por controlador
- Transmisión de los resultados de medición a través de bus de campo (Profi bus DP, Modbus), salidas analógicas, interfaz serie o Ethernet
La detección exacta de distintas fases en una tubería es necesaria en diversos sectores industriales. A menudo, los distintos productos se transportan por la misma tubería, pero cada uno se alimenta a un lugar distinto.
En aplicaciones en las que, por ejemplo, el producto A es expulsado por el producto B, la fase intermedia debe separarse por separado. En las fábricas de cerveza, por ejemplo, los distintos tipos de cerveza se embotellan uno tras otro, pero las fases previa y posterior circulan hacia el exterior y se realimentan al proceso de elaboración.
Los aspectos de seguridad también desempeñan un papel en aplicaciones con un alto potencial de riesgo. En concreto, la supervisión de la separación de fases en las tuberías multicomponente de la industria química no sólo proporciona información sobre la calidad del producto (mercancías entrantes), sino que también evita el llenado incorrecto de los tanques de almacenamiento y, por tanto, accidentes graves.
En la industria petroquímica, diferentes combustibles se transportan a través de distancias muy largas en una única tubería. En este caso, tanto la detección rápida de los distintos productos como el control de su calidad son primordiales.
La separación de dos fases puede llevarse a cabo en procesos por lotes. En este caso, los líquidos (por ejemplo, agua y aceite) se separan entre sí en función de sus propiedades físicas y químicas.
Ejemplo de aplicación 1: Productos orgánicos
Durante el proceso de fabricación de cosméticos, se produce una separación de fases en la que una fase salina que contiene mucha agua se separa de un producto preliminar. Esta fase inferior, rica en agua, se vierte a través de la planta de tratamiento de aguas residuales, donde se trata el agua. El precursor producido, la fase superior, sólo es biodegradable hasta cierto punto. Por lo tanto, es de suma importancia evitar que este material contaminante del agua entre en las aguas residuales. Para no contaminar el agua de las depuradoras, la identificación inmediata y fiable de la fase de preproducto es de máxima prioridad para evitar que se introduzca en el sistema de aguas residuales desconectándolo rápidamente.
En este punto no se pueden utilizar métodos de medición ópticos porque durante la separación de fases se pueden producir coloraciones diferentes. Además, la separación de fases puede dar lugar a la formación de una capa de mantillo, que se sabe que es crítica para la medición mediante efectos ópticos límite debido a los efectos de contaminación.
Ejemplo de aplicación 2: Biodiesel / glicerina
La glicerina es un subproducto de la producción de biodiesel. La mezcla de ambas sustancias se transporta en grandes tanques de decantación y después tiene varias horas para separarse. Los sensores LiquiSonic® suelen instalarse en la salida del tanque. Al reconocer la fase respectiva, se activa la válvula y el biodiésel y la glicerina pasan a la etapa de procesamiento posterior correspondiente. La fase intermedia vuelve al proceso de separación.
1.3 Separación de fases en el proceso continuo
En un proceso continuo, la separación de un flujo de proceso se controla mediante uno o varios sensores. En este caso, sólo se controla y se mantiene constante el valor de velocidad sónica característico de la fase respectiva.
La concentración de producto de la fase portadora en la alimentación fluctúa a menudo. Esto desplaza rápidamente la altura del límite de fase. Como resultado, la fase portadora podría ser arrastrada con el producto, lo que tiene un gran impacto en la pureza. En términos de tecnología de procesos, los líquidos se separan mediante una bomba en cada una de las dos líneas de salida. De este modo, por ejemplo, se puede controlar la separación continua de una mezcla de reacción.
Las ventajas de la tecnología de medición LiquiSonic® no sólo residen en el tiempo de respuesta extremadamente rápido de menos de 1 s, sino también en la conexión de hasta cuatro sensores a un solo controlador LiquiSonic®. Éste procesa todos los valores medidos y envía los datos al sistema de control de nivel superior.
Dependiendo del tipo de depósito y de los requisitos, son posibles diferentes variantes de instalación, que se muestran en el siguiente diagrama.
Variante de instalación 1
Los sensores se instalan con mayor frecuencia en el lateral del depósito. La necesidad del sensor central (punto de medición 2) depende de la aplicación y de las características de la fase intermedia.
Variante de instalación 2
Si sólo se utiliza un sensor con una longitud de hasta 4 m, se puede determinar el perfil de fase de todo el depósito. Montando el sensor en un carro móvil, por ejemplo, y en combinación con un sensor de desplazamiento, se pueden determinar los límites de fase exactamente a su altura actual.
Variantes de instalación 3 y 4
En depósitos en los que no se dispone de conexiones laterales o éstas pueden realizarse posteriormente, por ejemplo, doble camisa calefactable, los sensores se colocan directamente o mediante tubos de inmersión en el lugar correcto. Cuando se utilizan tubos de inmersión, la electrónica del sensor se sitúa a distancia, a una distancia de hasta 15 m fuera del depósito.
2. Sistema liquiSonic
2.1 LiquiSonic® 30
El sistema LiquiSonic® se compone de uno o varios sensores y un controlador. El sensor ultrasónico contiene la sección de medición ultrasónica y la medición de temperatura de alta precisión. Cada sensor funciona de forma independiente y puede utilizarse en diferentes aplicaciones. Las partes del sensor que entran en contacto con líquidos están fabricadas de serie en acero inoxidable DIN 1.4571.
El diseño robusto y totalmente encapsulado no requiere juntas ni "ventanas" para su uso y, por tanto, no requiere mantenimiento alguno. Diversas funciones adicionales integradas en el sensor, como el monitor de caudal y el control de húmedo/seco, aumentan considerablemente las ventajas para el cliente. La tecnología de alto rendimiento LiquiSonic® garantiza resultados de medición estables, incluso con una mayor proporción de burbujas de gas y una fuerte atenuación de la señal por el líquido de proceso.
La electrónica especial del sensor se encuentra en una carcasa cerrada de fundición a presión con clase de protección IP65. Si el espacio es limitado, pueden instalarse sensores con electrónica remota. El controlador 30 gestiona los datos de medición y se encarga de la visualización. Se maneja a través de la pantalla táctil de alta resolución. Gracias a la integración en red segura con servidor web incluido, el controlador puede manejarse alternativamente a través de un navegador utilizando un PC o una tableta.
El valor de visualización puede ajustarse a los valores de referencia internos mediante la función de ajuste. Los datos del proceso se actualizan cada 250 milisegundos. Si los valores medidos se mueven fuera del rango límite, esto se muestra en la pantalla y se emite una señal inmediatamente.
Los datos de medición pueden transmitirse a controladores, sistemas de control de procesos o PC a través de varias salidas analógicas o de relé libremente escalables, así como a través de diversas interfaces de bus de campo. Los datos de medición se almacenan en el completo libro de registro de datos. Hay 2 GB disponibles para información de proceso y 32 (opcionalmente 99) registros de datos de producto para diversos líquidos de proceso. Estos pueden leerse a través de la red o de la interfaz USB para su procesamiento en un PC. Además, se pueden crear fácilmente registros de procesos con fines de documentación. El controlador 30 también integra un libro de registro de eventos. En él se documentan eventos como un cambio manual de producto, cambios de configuración o mensajes de advertencia y estado.
2.2.2 Bus de campo
La opción de bus de campo ofrece la posibilidad de integrar el controlador en un sistema de control de procesos o de automatizar la secuencia del proceso mediante un controlador (PLC). Además de la transmisión de valores medidos como la concentración o la temperatura, también se pueden intercambiar parámetros y datos de control (por ejemplo, cambio de producto).
El controlador es compatible con diversos sistemas de bus de campo y sigue los estándares recomendados por las respectivas organizaciones de normalización. Las variantes más comunes son Modbus y Profibus DP.
3. Calidad y servicio
El entusiasmo por el progreso tecnológico es nuestra fuerza motriz para ayudar a dar forma al mercado del mañana. Ustedes, nuestros clientes, están en el centro de todo esto. Nos comprometemos a ofrecerles el máximo rendimiento. En estrecha colaboración con usted, seguimos el camino de la innovación, desarrollando la respuesta adecuada a su exigente tarea de medición o realizando adaptaciones personalizadas del sistema. La creciente complejidad de los requisitos específicos de las aplicaciones hace que sea esencial una comprensión exhaustiva de las interrelaciones e interacciones.
La investigación creativa es otro pilar fundamental de nuestra empresa. Los especialistas de nuestro equipo de investigación y desarrollo realizan valiosas aportaciones a la optimización de las propiedades de los productos, como la comprobación de nuevos diseños de sensores y materiales o la sofisticada funcionalidad de los componentes electrónicos, de hardware y de software. Nuestra gestión de la calidad SensoTech también acepta sólo el máximo rendimiento en la producción. Contamos con la certificación ISO 9001 desde 1995. Todos los componentes de los dispositivos se someten a diversos procedimientos de prueba en las distintas fases de producción; los sistemas se someten a un procedimiento de rodaje en nuestras instalaciones. Nuestra máxima: máxima funcionalidad, resistencia y seguridad.
Todo esto sólo es posible gracias al compromiso y la marcada conciencia de calidad de nuestros empleados. Debemos nuestro éxito a su extraordinaria experiencia y motivación. Juntos, con pasión y convicción, trabajamos con una excelencia sin igual.
Cultivamos las relaciones con nuestros clientes. Como nuestros aparatos no requieren mantenimiento, podemos centrarnos por completo en sus preocupaciones en lo que respecta al servicio y ayudarle activamente con asesoramiento profesional, una cómoda instalación in situ y formación para el cliente. Durante la fase de diseño, analizamos su situación directamente in situ y realizamos mediciones de prueba si es necesario. Nuestros dispositivos de medición son capaces de alcanzar la máxima precisión y fiabilidad incluso en condiciones desfavorables. Incluso después de la instalación: estamos a su disposición, nuestros tiempos de respuesta son cortos gracias a las opciones de acceso remoto adaptadas específicamente a sus necesidades.
En el marco de nuestras cooperaciones internacionales, formamos para nuestros clientes un equipo interconectado a escala mundial que garantiza un asesoramiento y un servicio óptimos más allá de las fronteras nacionales, por lo que concedemos gran importancia a una gestión eficaz de los conocimientos y la cualificación. Nuestros numerosos representantes internacionales en todos los mercados geográficos clave del mundo pueden aprovechar los conocimientos especializados de la empresa y actualizar continuamente sus competencias en programas de formación relacionados con la aplicación y la práctica. La proximidad a los clientes de todo el mundo: un factor clave de nuestra exitosa presencia global junto con nuestra amplia experiencia en el sector.
Innovadora tecnología de sensores
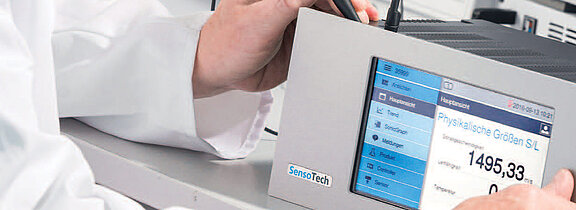
SensoTech es el especialista en análisis y optimización de procesos de ingeniería de procesos en líquidos. Desde nuestra fundación en 1990, nos hemos convertido en la empresa líder en dispositivos de medición para la determinación en línea de concentraciones en líquidos. Nuestros sistemas de análisis marcan tendencia en todo el mundo.
Ingeniería innovadora made in Germany, basada en el principio de medición de la velocidad absoluta del sonido durante el proceso. Un método que hemos perfeccionado hasta convertirlo en una tecnología de sensores altamente precisa y excepcionalmente fácil de usar.
Además de la medición de la concentración y la densidad, las aplicaciones típicas incluyen la detección de fases o la supervisión de reacciones complejas como la polimerización y la cristalización. Nuestros sistemas de medición y análisis LiquiSonic® garantizan una calidad óptima de los productos, la máxima seguridad de las instalaciones o reducen los costes mediante una gestión eficaz de los recursos en una amplia gama de sectores, como las industrias química y farmacéutica, la siderurgia, la tecnología alimentaria, la ingeniería mecánica y de instalaciones, la ingeniería de automoción y otros.
Queremos que aproveche al máximo el potencial de sus instalaciones de producción en todo momento. Los sistemas SensoTech ofrecen resultados de medición de gran exactitud, precisión y reproducibilidad, incluso en condiciones de proceso difíciles. Y todo ello en línea y sin muestreo crítico para la seguridad, inmediatamente disponible para su sistema de automatización. Además, todos los parámetros del sistema pueden personalizarse con potentes herramientas de configuración para que pueda reaccionar de forma inmediata y sencilla a los cambios.
Ofrecemos una tecnología excelente y sofisticada para mejorar sus procesos de fabricación y somos su socio para soluciones sofisticadas, a menudo inimaginables en su sector, para sus aplicaciones, por específicas que sean. Cuando se trata de líquidos, establecemos los estándares.