Inline measurement of acid strength and iron salts in the pickling bath
Measuring density and concentration in liquids with ultrasound offers some special advantages compared to other methods. Here are the key aspects:
1. High precision and reliability
- Ultrasonic measurements are extremely accurate, as the speed of sound in a liquid directly correlates with its density and concentration.
- The measurements are reproducible and stable, even under fluctuating process conditions.
2. Real-time measurement for continuous processes
- Unlike laboratory analyses, the measurement takes place inline and in real-time. This allows processes to be adjusted immediately
- This is particularly advantageous in the chemical industry, food production, or metal processing, where quick reactions to concentration fluctuations are required
3. Low maintenance and durable
- No moving parts mean less wear and a long lifespan
- Sensors are mostly robust against deposits, dirt, and aggressive media
4. Independent of optical influences
- Unlike optical methods, ultrasonic sensors are insensitive to turbidity, color, or gas bubbles
- This makes the method particularly suitable for difficult process conditions, such as in petrochemicals or heavily contaminated liquids
5. Versatile use
- Measurements are possible at high temperatures, pressures, and in aggressive media
- Particularly valuable for industries such as Chemistry, Pharmaceuticals, Oil & Gas, Food, Metal Processing and Solvent Recovery
6. Combination with temperature measurement for more precise results
- Since the speed of sound is also temperature-dependent, ultrasonic sensors are always equipped with integrated temperature compensation equipped
- This allows for even more accurate concentration measurements
7. Direct concentration determination for complex liquids
- In addition to pure density measurement, ultrasonic technology can determine specific concentrations of multicomponent systems determine, for example, mixtures of water, alcohol, acids, or oils
- Particularly useful in chemical production, monitoring of alkaline gas scrubbers and metal processing (pickling solution, electroplating, cleaning agents)
Conclusion
Measuring with ultrasound is a precise, reliable, and low-maintenance technology, which is ideal for industrial process monitoring suitable. It impresses with its robustness, real-time capability, and versatility, which makes it superior to many other measurement methods.
LiquiSonic® - Unrivaled good
Conventional measurement method: Laboratory samples are analyzed offline using titration or spectroscopy, leading to blind operations due to the lack of continuous monitoring – this poses a high risk of rejects and causes correspondingly high costs.
Measuring with the LiquiSonic: Continuous inline measurement with our measurement system, the ultrasonic measurement, and the conductivity measurement guarantee uninterrupted precise values with simultaneous measurement of acid and iron concentration
Material: Acid-resistant plastic coating
Highlight: Maintenance-free due to the perfect material selection and the individual and optimal sensor design, 8 to 12+ years without maintenance
What errors can occur during the pickling process?
During the pickling process with conventional offline measurement methods, three problems frequently occur:
- Excessive pickling time – The batch becomes unusable.
- Insufficient pickling time – Electroplating is no longer possible.
- Inaccurate pickling acid dosing Delayed offline analyses lead to quality fluctuations.
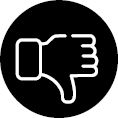
LiquiSonic® reduces errors in the pickling process
LiquiSonic® ensures precise analysis of pickling bath concentrations with continuous data recording. The replenishment of fresh acid can be precisely controlled to maintain the optimal concentration of the pickling bath and ensure the best pickling results. In addition, under- and overdosing of hydrochloric acid are avoided. LiquiSonic® reduces time-consuming laboratory measurements and replaces complex sampling. Production costs are reduced.
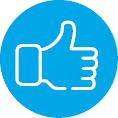
Installation of LiquiSonic® measurement technology in the pickling bath process
The LiquiSonic® measurement technology is installed in the transport lines (usually DN80) or in the bypass of the pickling baths. It has also proven itself in the rinse bath and in the fresh acid supply LiquiSonic® proven. The robust sensor construction and the choice of special materials, such as Halar or PFA, ensure long system process runtimes.
The use of the installation adapter simplifies the installation of the LiquiSonic® pipe sensor DN80 and the associated conductivity sensor into a DN80 piping system. The total length of the measuring section with adapter is 0.7 m.
Typical measuring ranges:
Concentration of free HCl: 0 - 250 g/l
Concentration of Fe: 0 - 140 g/l
Temperature range: 60 - 95 °C
Other pickling acids? Other measuring ranges? No problem for LiquiSonic®.
Contact us!
Permanent display of concentration in the controller
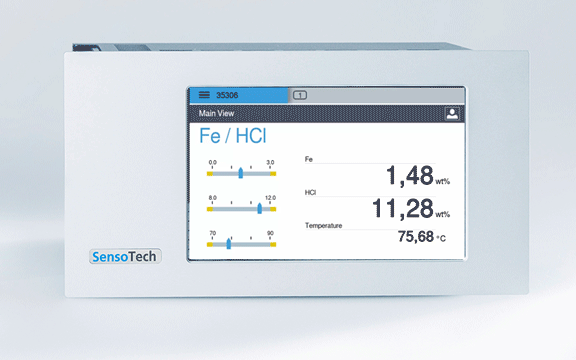
Downloads for inline pickling bath monitoring
FAQ & Further information
A pickling bath is a tank or container filled with an acidic solution used to remove oxide deposits, rust, and other impurities from the surface of steel and other metals. This bath is a key component of the pickling process and ensures a clean and smooth surface before further processing such as galvanizing, coating, or painting.
Components of a pickling bath
-
Acidic solution
-
The type of acid used depends on the material to be processed and the desired cleaning effect:
-
Hydrochloric acid (HCl) - Fast-acting, often used for pickling steel
-
Sulfuric acid (H₂SO₄) - More economical, but slower, often heated for better efficiency
-
Nitric acid-hydrofluoric acid (HNO₃ + HF) - Used for stainless steel to remove oxides and passivate surfaces
-
Phosphoric acid (H₃PO₄) - Used when a protective phosphate layer is required
-
-
-
Inhibitors (optional)
-
Additives that reduce acid attack on base metal while allowing removal of scale and rust
-
-
Temperature control system
-
Some pickling baths are heated to improve reaction efficiency, especially when Pickling with sulfuric acid
-
-
Rinsing and neutralization (optional)
-
After pickling, the steel is often passed through a rinse bath with water and sometimes an alkaline solution (e.g., sodium carbonate) to neutralize any acid residues
-
-
Ventilation and fume extraction
-
Acid baths produce fumes that can be hazardous, which is why industrial facilities are often equipped with scrubbers or ventilation systems
-
How a pickling bath works
-
Steel or metal parts are immersed in the pickling bath
-
The acid reacts with the oxides and dissolves them, cleaning the surface
-
The material is rinsed with waterto remove acid residues
-
If necessary, it is neutralized with an alkaline solution
-
The cleaned steel is dried and sent for further processing (e.g., galvanizing, painting)
Types of pickling baths
-
Static pickling baths: For batch processing of steel parts, sheets, or coils
-
Continuous pickling baths: Used in high-speed steel production lines where the metal runs continuously through several acid baths
-
Electrolytic pickling baths: Here, electric current is used along with acid to improve scale removal
Ecological aspects
-
Acidic waste must be treated before disposal
-
Spent acid can be regenerated (especially hydrochloric acid)
-
Fume extraction systems are required for worker safety
Pickling is a chemical process used to remove impurities such as oxides (scale), rust, and other contaminants from the surface of steel. It is commonly used in steel production and manufacturing to ensure a clean, smooth surface for further processing such as galvanizing, painting, or coating.
Step-by-step pickling process
-
Pre-cleaning (optional)
-
Before pickling, the steel can be mechanically cleaned or degreased to remove oils, dirt, and loose scale
-
-
Acid bath (pickling)
-
The steel is usually immersed in a bath with an acidic solution:
-
Hydrochloric acid (HCl) - Fast and efficient, commonly used in modern pickling plants
-
Sulfuric acid (H₂SO₄) - More cost-effective, but slower and requires heating
-
Mixed or organic acid baths - For special applications with lower environmental impact
-
-
The acid reacts with the oxides and scale, removing them from the surface
-
-
Rinsing
-
After pickling, the steel is thoroughly rinsed with water to remove acid residues
-
-
Neutralization (optional)
-
Some processes include a neutralization step with an alkaline solution (e.g., sodium carbonate or sodium hydroxide) to prevent acid carryover
-
-
Passivation (optional)
-
A passivation layer (e.g., a phosphate or chromate treatment) can be applied to prevent immediate rusting
-
-
Drying and finishing
-
The cleaned steel is dried and can be further processed, e.g., by galvanizing, painting, or cold rolling
-
Types of pickling
-
Batch pickling: Steel is processed in batches, typically used for coils, sheets, and finished parts
-
Continuous pickling: Used for high-speed processing of steel strips in large production lines
-
Electrolytic pickling: The removal of oxides is improved using electric current
Summary
-
In pickling, hot-rolled steel is immersed in a solution called pickling liquor to remove surface impurities and iron oxide scale
-
The solution used is usually hydrochloric acid, but for high-carbon steels, additional acids such as nitric acid, sulfuric acid, or hydrofluoric acid may be required.
-
Pickling removes 1-3% of the steel mass, which makes processing and painting more difficult.
-
The remaining pickling liquid, called pickling sludge, is often neutralized with a base and disposed of, but can also be used to recover useful products such as hydrochloric acid and iron oxide.
The monitoring of acid strength in a pickling bath is crucial for maintaining efficiency, controlling metal dissolution rates, and ensuring product quality. There are several methods for determining the strength of an acid solution:
Sound velocity measurement (ultrasound method)
- Principle: Measures the sound velocity in an acidic solution to determine concentration
- Method: An ultrasonic sensor sends a sound wave through the liquid; the transit time is recorded and compared with calibration data
- Best suited for: Continuous real-time monitoring of acid concentration in industrial pickling baths
- Advantages:
✔️ Non-destructive and fast - No sample extraction required
✔️ Highly precise - No interference from dissolved metal ions
✔️ Real-time monitoring - Suitable for automated process control - Disadvantages:
❌ Requires initial calibration for each type of acid and temperature (included in LiquiSonic)
pH measurement
- Principle: Measures the hydrogen ion concentration in the solution
- Method: A pH meter or indicator strips indicate the acidity level
- Best suited for: Quick, rough estimation of acid content
- Advantages:
✔️ Simple and fast - Requires minimal equipment
✔️ Low cost - Simple pH strips or meters are affordable - Disadvantages:
❌ Not accurate for strong acids - pH value does not provide exact acid concentration
❌ Influenced by temperature and impurities
❌ Extremely high maintenance and material costs (ongoing costs)
❌ Unreliable measurements, as often worn out and calibration needed after just a few days
Measurement of specific gravity
- Principle: The concentration of an acid correlates with its Density (g/cm³)
- Method: With a Hydrometer is used to measure the specific weight of the solution, which is then compared with reference tables
- Best suited for: Quick field tests of H₂SO₄ and HCl baths
- Advantages:
✔️ Fast and easy - no chemical reagents required
✔️ Non-destructive - no need to neutralize or discard samples - Disadvantages:
❌ Does not distinguish between free acid and dissolved metal salts
❌ Temperature dependent, requires corrections
Acid titration
- Principle: Uses a Neutralization reaction with a known base (e.g. NaOH) to determine the content of free acid
- Method: A measured sample is titrated with Sodium hydroxide (NaOH) and an indicator to determine the acid concentration
- Best suited for: Accurate testing of acid concentration in the laboratory
- Advantages:
✔️ Highly precise - Determines the exact concentration of free acid
✔️ No interference from dissolved metal content - Disadvantages:
❌ Time-consuming - Requires laboratory equipment and qualified personnel
❌ Required sample - Destructive testing method
❌ No inline measurements and therefore time delay and trial runs
❌ Operator error possible and staff training needed
Measurement of conductivity
- Principle: Measures the electrical conductivity of the solution, which increases with the acid concentration
- Method: A conductivity meter provides a measurement that correlates with acid strength
- Best suited for: Continuous monitoring of HCl and sulfuric acid solutions (with appropriate calibration)
- Advantages:
✔️ Fast and easy - Provides real-time measurements
✔️ Non-destructive - no sample loss - Disadvantages:
❌ Affected by dissolved metal ions and requires frequent calibration
❌ Not suitable for all acids (e.g., oxidizing acids)
❌ No distinction between acid and metal content
- Pickling is essential for preparing metal surfaces for further processing, such as cold working, welding, or painting
- Pickling helps remove mill scale and iron scale from hot-rolled steel, improving surface quality and reducing the risk of defects
- Pickling is widely used in various industries, such as construction, automotive, and manufacturing
- Pickling can also be used to remove surface contaminants from other metals like stainless steel and aluminum
- The pickling process can help improve the corrosion resistance of metal surfaces
- Monitoring the acid concentration in the pickling bath is crucial for the effectiveness of the pickling process
- The pickling bath should be regularly cleaned and descaled to prevent the buildup of iron oxide and other contaminants
- The use of automatic monitoring systems can help optimize the pickling process and reduce waste